


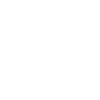


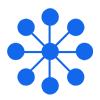
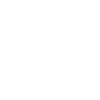


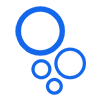
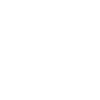


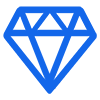
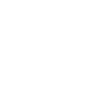
<script> var _hmt = _hmt || []; (function() { var hm = document.createElement("script"); hm.src = "https://hm.baidu.com/hm.js?2632353fc1e8e1de5091a3e7301dfade"; var s = document.getElementsByTagName("script")[0]; s.parentNode.insertBefore(hm, s); })(); </script>
2020 官网升级中!现在您访问官网的浏览器设备分辨率宽度低于1280px
请使用高分辨率宽度访问。
Suryee Technology develop a series of Arc spraying flux cored welding wires, The product has high purity, high temperature oxidation resistance, corrosion resistance, high wear resistance, and excellent performance. It is widely used in mechanical repair and manufacturing processes such as circulating fluidized boilers, coal powder furnaces, steel plant converter hoods, shafts, and fan blades.
The company has been specializing in the development, production and sales of arc spraying powder core wire, wear-resistant plate overlay welding powder core wire, laser cladding materials, anti-corrosion materials and processes for 15 years.
SAM®-Amorphous High Hardness and Wear Resistant Flux Cored Welding Wires
SAM®-Amorphous high hardness and wear-resistant coating technology,can preparation of high-performance coatings containing nanocrystals on the surface of parts requiring high wear and corrosion control such as CFB circulating fluidized bed furnace 4-tube, steel plant converter hood.
SAM spraying layer containsamorphous phase,amorphous transformation occurs under 500~600℃℃ its wear and corrosion resistance isbetter than Commonly used arc spra-ying material at home and abroad.The relative wear resistance is morethan 25 times that of 20G, and hashigh bond strength (>50MPa), hard-ness value >65HRC, good thermalshock resistance.The porosity of thecoating is very low, and the oxide inthe coating is very little.
SOR-Stainless steel anti high temperature oxidation
SOR is good at resistance to hightemperature oxidation, sulfur andheat corrosion. lt's a high degree ofhardness.lt can replace NiCrTicoating(Cr>40%) which is theleading product of its kind. lt'shigh cost performance.
SOR thermal spraying powder corewire components mainlyinclude:Cr>40%, containing Ti, B, Ni and asmall amount of RE.The arc sprayinglayer bond strength is more than50MPa.The coating hardness ismore than 55HRC(Vickers hardness645~800 HV0.1 conversion value).The porosity is low, oxides in thecoating is very few, the thermal shockresistance is good.The resistanceto high-temperature erosion andoxidation are good.
SOR thermal spraying powder corewire is widely used in the protectionof pulverized coal furnaces, conve-rter hoods and fue ducts which ischaracterized by oxidation,abrasionand sulfur corrosion resistance.
Waste incinerator is an effective way to treat domesticwaste,with the characteristics of reduction,harmlessnessand resourcefulness. Corrosion of the heating surface ofwasteincineration boilers is a serious problem and is acommon problem, reduces the service life greatly, one ofthe important bottlenecks that restrict its development.The corrosion mechanism is mainly due to the presenceofCl, S and alkali metals in the incinerated waste corrosioncaused byCl,S chemical gas corrosion and low meltingpoint alkali metal salt melt corrosion.Especially highparameterization,which exacerbates the problem of hightemperature corrosion, is refected in: 1.The gradualincrease in the calorifc value of waste,far beyond theearly construction was designed for the rated value. 2.Thedesign value is 1500kcal/kg,and now the frst-tier citieshave reached more than 2000kcal/kg. 3.In recent years,waste incineration boilers to large-scale,highparameter development.
Surface melting technology is to make the alloy elementsand the substrate melt through heating to form ametallurgicalcombination, so as to prepare a thin surfacelayer with various excellent properties. A layer of anti-corrosion and wear-resistant alloy layer is melted on thesurface of the substrate,which can not only retain theoriginal mechanical properties of the substrate, but alsogreatly enhance the anti-corrosion, wear and impactresistance of the surface and prolong the service life ofthe product.
At present,our company adopts a variety of meltingtechnologyincluding:induction surface melting, lasersurface melting, thermal spraying and surfacingmelting, etc., to meet the cladding requirements of manykinds of multi-functional parts surface anti-corrosionand wear-resistant layer.